Il processo produttivo de La Metallurgica
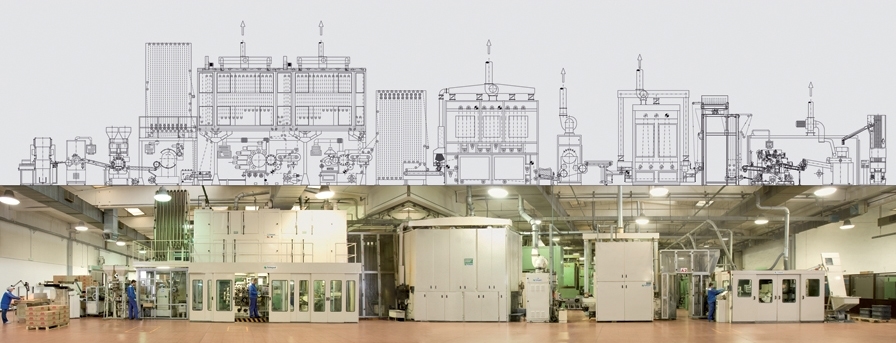
Il processo produttivo di un tubetto deformabile in alluminio è una sequenza di operazioni tecnologiche molto diverse tra loro. E' un processo continuo e completamente automatico: dal caricamento delle pastiglie di alluminio nella pressa fino alla scatolatrice dove i tubetti finiti vengono posti nelle scatole, i tubetti non necessitano di essere manipolati ma vengono trasportati attraverso una serie di macchine collegate tra loro con passaggio automatico del semilavorato tra una macchina e la successiva.
Processo meccanico
Verniciatura interna
Processo di stampa
Fine linea
Processo meccanico
(pressa, tornietto, sistema eliminazione trucioli, polmoncino fasatore)
Il processo inizia con il carico delle pastiglie di alluminio ricotte, provenienti dal reparto di burattatura, nell'alimentatore della pressa; tali pastiglie, tramite elevatore e selezionatore, vengono trasportate automaticamente nella pressa orizzontale dove subiscono l'operazione di estrusione a rimonta a freddo.
La pastiglia viene compressa tra il puntale e la matrice e la pressione esercitata è tale da generare una deformazione plastica dell'alluminio.
Si creano inizialmente spalla e bocchello del tubetto mentre l'alluminio eccedente scorre nella parte circonferenziale libera tra matrice e puntale, formando il corpo tubetto.
Lo scorrimento così rapido del materiale dà origine, in un singolo colpo, al semilavorato con la forma di tubetto e ad un aumento della temperatura dello stesso fino a raggiungere quasi i 200 °C; il semilavorato che arriva dalla pressa viene poi trasferito attraverso un trasportatore automatico al tornietto.
In questa seconda macchina il semilavorato viene filettato, intestato e tagliato alla lunghezza desiderata. Al termine di queste operazioni il tubetto è dimensionalmente finito. Viene inoltre lucidata la spalla del tubetto grazie ad una spazzola rotante in modo da renderla perfettamente liscia e lucente.
La Metallurgica è dotata inoltre di sistemi automatici per l'eliminazione di eventuali trucioli generatisi in fase di estrusione.
Tutti gli eventuali scarti e sfridi di produzione sono estratti meccanicamente ed aspirati dal sistema centralizzato di raccolta scarti; tutto l'alluminio di scarto è poi riciclabile al 100%.
Queste prime operazioni del processo di formatura del tubetto in alluminio sono principalmente operazioni meccaniche che definiscono qualitativamente le caratteristiche dimensionali del tubetto finito.
Verniciatura interna
(forno di ricottura, verniciatrice interna, forno di polimerizzazione, accumulatore)
Proseguendo lungo la linea nell'analisi del processo produttivo, il trasportatore di scarico del tornietto adagia il semilavorato su un piccolo accumulatore che serve da unione tra le macchine che svolgono il processo meccanico appena descritto ed il seguente processo di ricottura dove il tubetto diviene deformabile a temperature superiori ai 400 °C; il materiale del semilavorato infatti, a seguito dell'operazione di estrusione e dunque alla deformazione plastica descritta in precedenza, si è ricristallizzato producendo un incrudimento, per eliminare il quale è necessario raggiungere tali temperature nei forni di ricottura al fine di ridare malleabilità al tubetto stesso.
Inoltre il calore all'interno del forno è in grado di eliminare completamente tutti quei residui di lubrificante utilizzato nel processo di estrusione che eventualmente fossero ancora presenti, rendendo il tubetto estremamente pulito ed igienico.
Il tubetto è così pronto per passare nella macchina di verniciatura interna che garantisce al tubetto quella protezione interna per essere riempito praticamente da qualsiasi tipo di prodotto.
La verniciatrice applica lo strato protettivo attraverso delle pistole il cui movimento è il risultato di una rotazione e contemporaneamente di una traslazione.
Il tubetto viene poi polimerizzato ad una temperatura variabile a seconda della vernice utilizzata, approssimativamente intorno ai 300 °C.
Le due operazioni appena descritte sono estremamente importanti; influiscono infatti sulla resistenza del tubetto agli agenti aggressivi e sulla capacità del tubetto di mantenere inalterate le proprietà organolettiche del prodotto contenuto.
Il passo successivo a queste operazioni è un altro accumulatore che trasferisce il tubetto alle macchine di stampa, fungendo da polmone nel caso di qualche fermo linea.
Processo di stampa
(macchina di fondo, macchina litografica, forni di appassimento ed essiccazione)
La prima macchina del processo di stampa è la macchina di fondo che applica, per contatto, uno strato di smalto esterno sulla superficie del tubetto.
Il tubetto viene quindi trasferito in un forno di appassimento dove lo smalto viene asciugato ad una temperatura compresa tra i 110°C ed i 140°C. Il tubetto smaltato ed asciugato giunge poi alla macchina di stampa dove vengono applicati gli inchiostri con metodo off-set per ottenere la litografia desiderata. Anche questa operazione è seguita da un forno, detto forno di essiccazione, dove gli inchiostri si incorporano con lo smalto. La temperatura in questo caso va dai 140°C ai 170°C. Ma questo è il processo tradizionale; La Metallurgica è andata oltre con...la stampa digitale DigIt.
Fine linea
(accumulatore, leak control, capsulatrice, masticiatrice, scatolatrice)
Il fine linea è costituito da più macchine: l'accumulatore, il controllo perdite, la capsulatrice, la masticiatrice e la scatolatrice. Il controllo perdite, detto anche leak control, è presente su tutte le linee de La Metallurgica e verifica al 100% la perfetta tenuta del tubetto.
Questa macchina dispone di un sistema di trasporto molto avanzato che muove il tubetto secondo una legge di velocità variabile, fermando il tubetto nella stazione di lavoro. In questa stazione, un sofisticato sistema in grado di controllare eventuali perdite di pressione, verifica la presenza di tagli o fori sull'intera superficie del tubetto e sulla membrana per mezzo di aria controllata immessa nel tubetto ad una pressione stabilita ed elimina i tubetti difettosi.
La capsulatrice avvita la capsula sul tubetto e, se necessario, applica l'inserto di plastica. Per particolari esigenze, sono disponibili sulla medesima macchina ulteriori applicazioni quali ad esempio l'applicazione del sigillo di garanzia od eventuali controlli qualitativi.
La masticiatrice applica l'anello di mastice alla bocca di riempimento del tubetto, essendo un'ulteriore garanzia di tenuta una volta riempito e chiuso. L'applicazione del mastice viene eseguita simultaneamente su due tubetti per mezzo di due unità centrifughe. Una volta masticiato, il tubetto viene trasportato per mezzo di un trasportatore di fronte alla scatola nella quale deve essere contenuto.
Nella scatolatrice, un sensore conta i tubetti che passano, controlla la loro introduzione nella scatola, fila per fila, fino a che la scatola non sia completa. I tubetti, automaticamente spinti all'interno della scatola attraverso degli spingitori sono così pronti per i controlli qualitativi ed il versamento a magazzino, disponibili per la spedizione una volta impilate le scatole sui bancali ed i bancali avvolti in film plastico estensibile.